機能しない生産管理システム
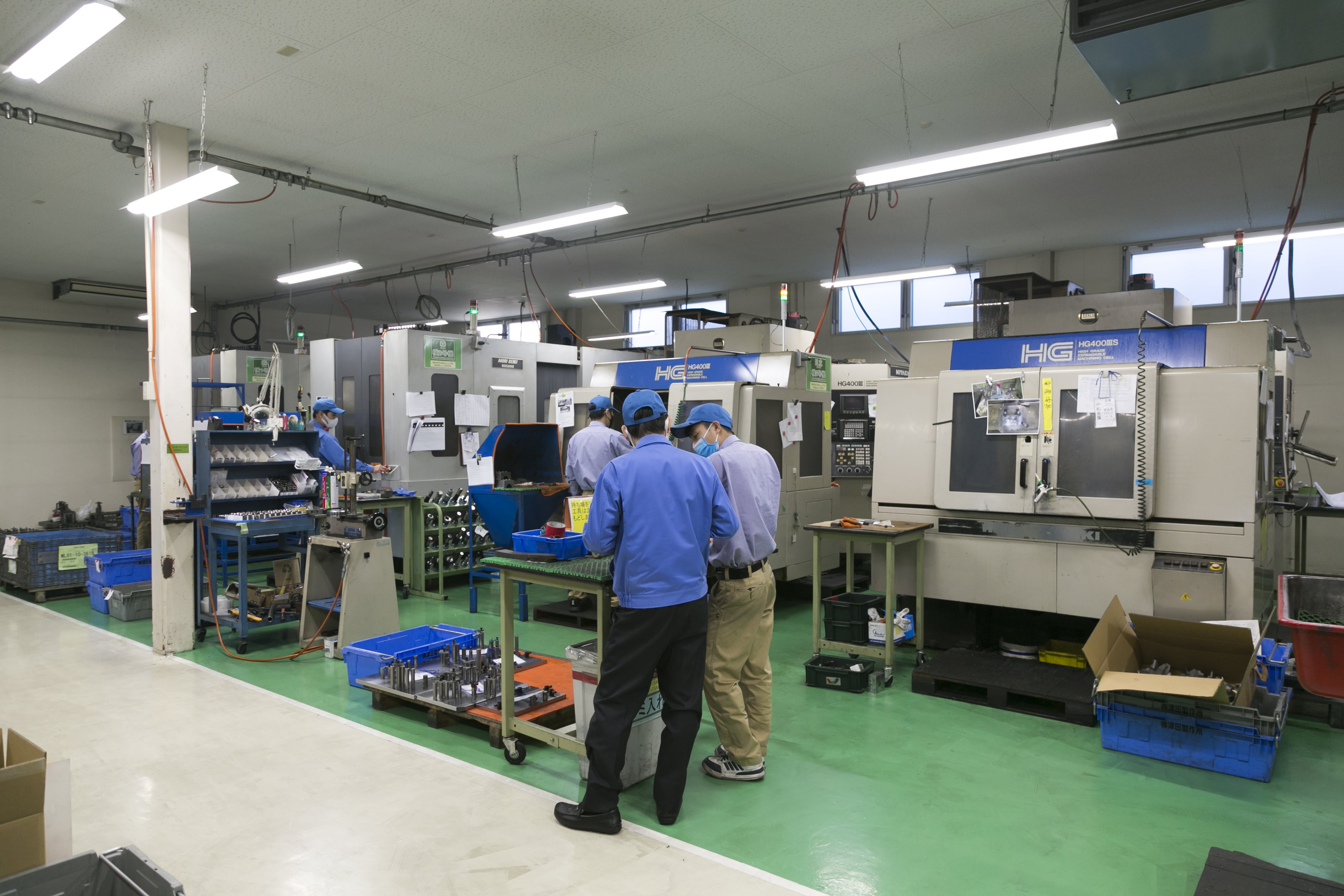
定期的に東京に足を運び、最新の技術や情報をリサーチしているという津田社長は、かなり早い段階で、「中小企業もAIやIoTを使わないと取り残される」と感じていた。しかし、そこにはリスクもある。
「最新の技術を導入するには、当然ながら資金と時間と人の先行投資が必要となる。そして、それが必ず成功するという保証はどこにもなく、全てが水の泡になる場合もあります。しかし、何もしなければ取り残されてしまいます」
このようなジレンマを抱えながら、津田社長は2014年から生産管理システムを導入し、工場内の機械の稼働状況を把握しようとした。しかし、
「そこから上がってくる情報は不正確で使えませんでした。なぜなら人間が入力するから。例えば、機械の稼働時間が実際は『2時間17分』だったとしても、現場の社員は『2時間』とアバウトに生産管理システムに入力してしまう。実際の稼働時間と、システムに登録された稼働時間に大きなズレが生じていたんです。これでは見積もりに反映させる正確なデータとして活用することができません。何度も社員に『正確な稼働時間を入力するように』と指導したのですが、なかなか正確なものは出てきませんでした」
機械の稼働率も、トラブルも把握できず・・・
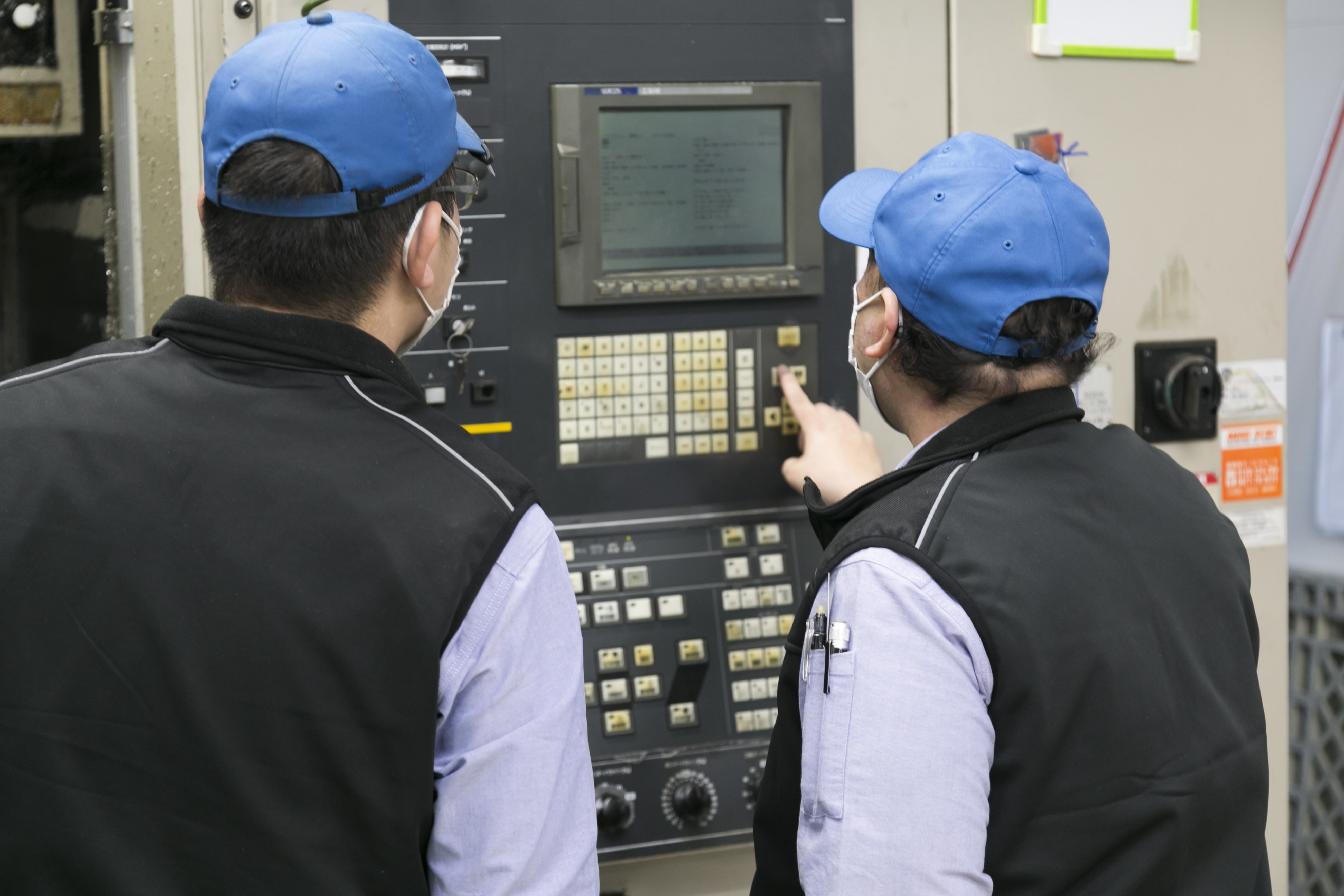
当時のことを、小林部長はこう振り返る。
「IoT化する前は、社長から、『小林、工場の稼働状況はどうなっている?』と聞かれて、「…工場から音が聞こえているので、動いてますよ」と冗談交じりに答えていました。それくらい、私の方でも把握のしようがなかったんです」
さらに、こんなこともあったという。
「以前は、機械トラブルを表す赤ランプが灯っても、すぐに把握することができませんでした。夕方になって、『実は、今日は昼からずっと赤ランプが点いて、機械が止まっていたんです』と、担当者から報告を受けるようなこともありました」
しかし、IoT化した後はそのような問題もなくなった。
「今はモニターを見れば、全ての機械の稼働状況がわかるようになりました。アラームの赤ランプで表示されると、すぐに係長が工場に駆け下りていき、対処できます。そういったことに対するスピード、レスポンスが早くなり、大変助かっています」
社員のためのIoTだが、最初は歓迎されなかった
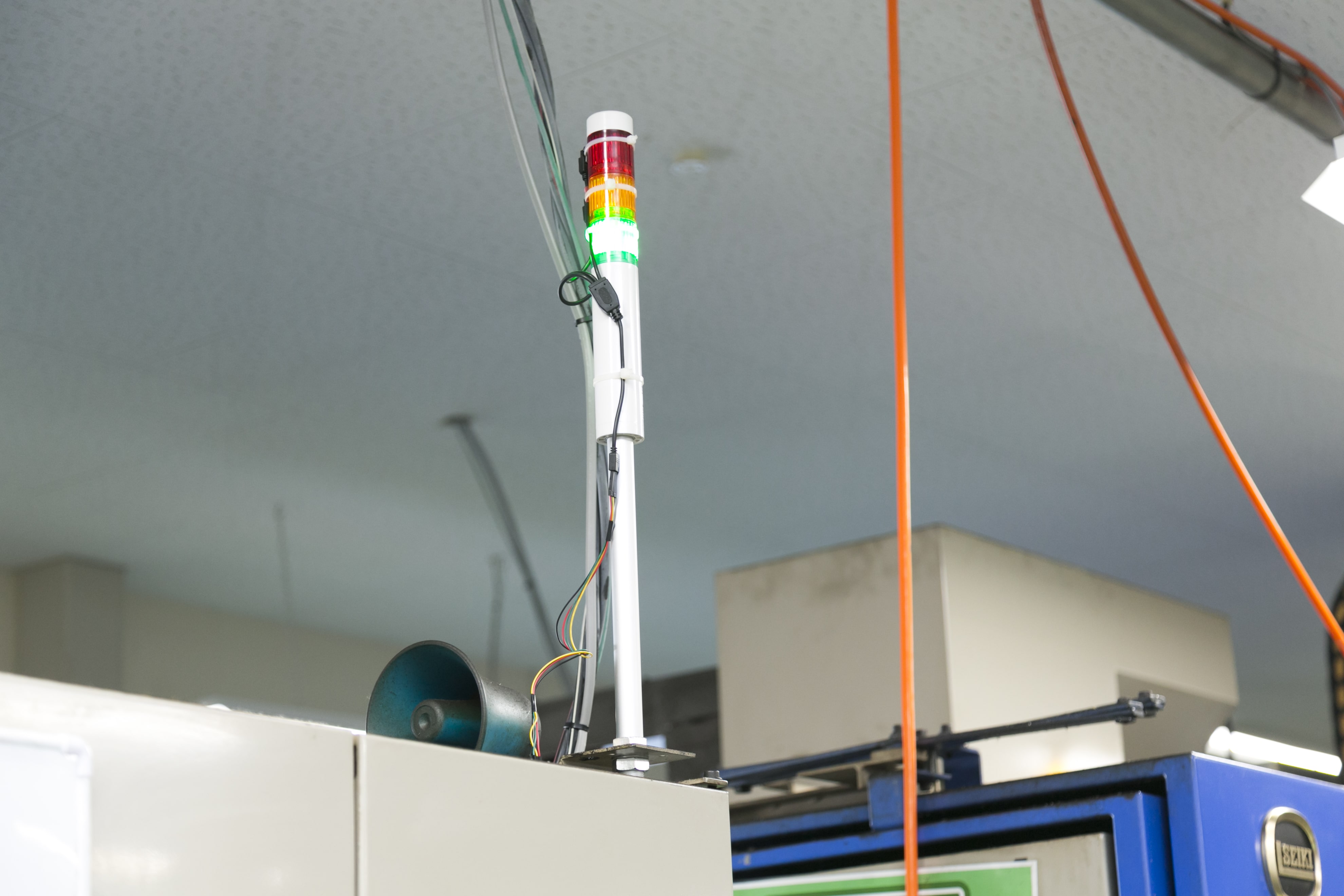
生産管理システムの導入が不調に終わってからしばらく経って、津田社長はある勉強会で「ひろしまサンドボックス」の取り組みに誘われ、参画を決定した。
津田製作所がIoTの導入するにあたって、まず着手したのが機械の稼働率の把握である。各機械の稼働状況を示す三色のライト(緑→稼働中、黄色→停止中、赤→アラーム・トラブル発生)のそれぞれに、光センサーを取り付けた。そしてその点灯状況を、現場と管理者用に設置したモニターで把握できるようにしたのだ。
「IoTによって生産性向上になれば、仕事の正確性が上がり、社員さんの負担を減らすことができます」
津田社長には、社員にとって働きやすい現場にしたいという狙いがあった。
「しかし、新しいものを取り入れることは、必ずしも社員から歓迎されません。抵抗感を示す者もいれば、全く関心を示さない社員もいます」 このような状況でスタートした津田製作所のIoT化。早速、津田社長は生産稼働率のデータを経営会議に持ち込み、管理者や社員たちに公表した。
「導入した当初は、社員たちのリアクションはほとんどありませんでした。稼働率が上がっても下がっても、『まあ、こんなもんでしょう』という感じでした」
会社のIoTの取り組みに興味を示さない社員たちだったが、約2年の取り組みの中で、徐々にその意識が変わり始めたそうである。
データを見ることで管理職の意識と発言内容が変わった!
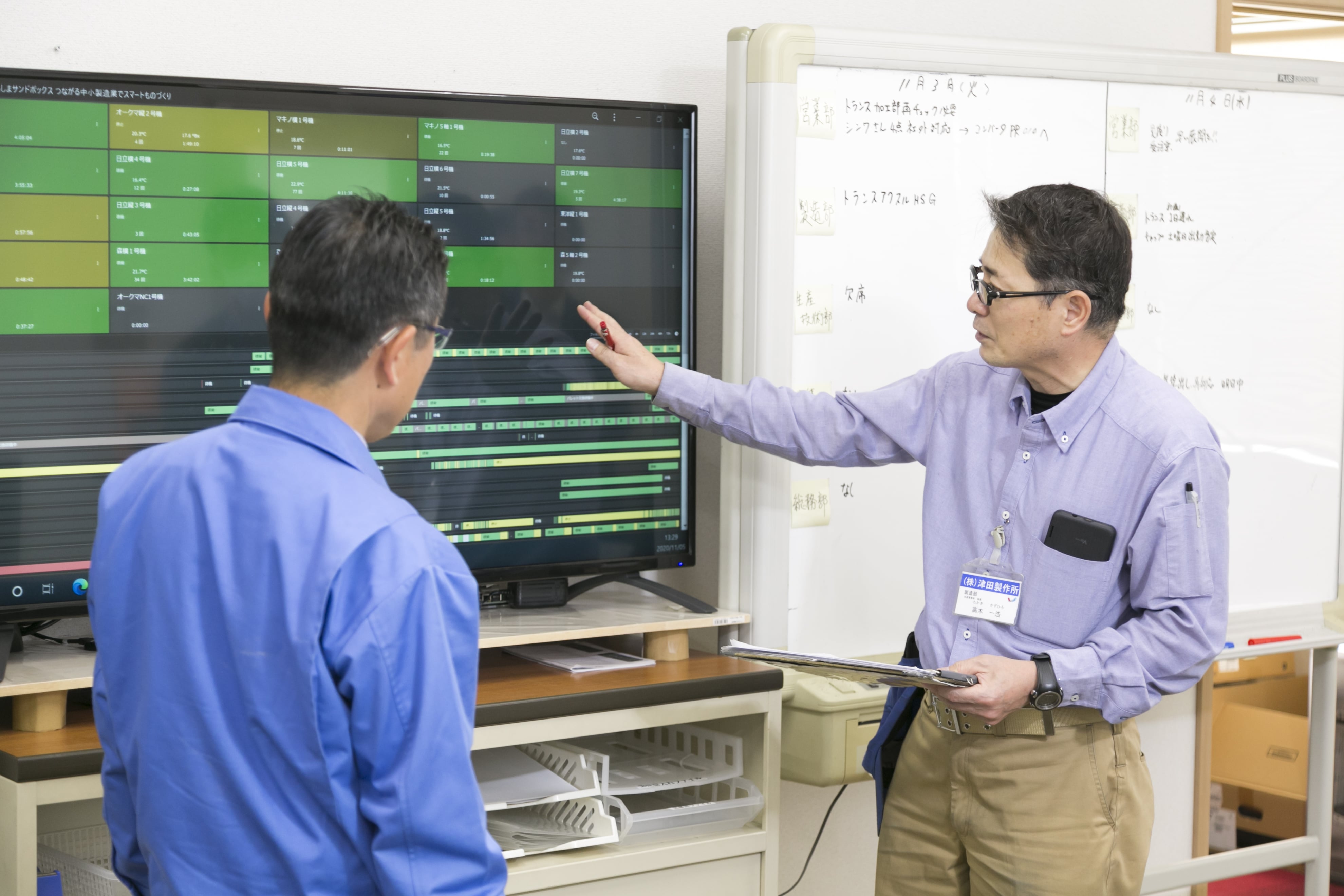
「次第に管理者の間から、『なんでこんなに頑張っているのに、稼働率が上がってないんだろう?』
とか、『あんなにヘトヘトになるまでやったのに、なぜ計画した稼働率の半分しか達成してないんだ?』といった声が出るようになりました。それまでは感覚的なもので判断していたものが、具体的な数字で管理できるようになって、管理者たちの意識が変わってきたんです。『どうやったら稼働率を上げることができるだろう?』といった声が、管理者たちの間から出るようになりました。1年前と比べると大きな変化です」
小林部長はこの変化が、さらに広がることを期待している。
「確かにIoTを導入してから管理者層言うことが変わってきました。今後は、一般社員も同じような意識を持ってくれたら、と期待しています。そうすれば、我が社はもう一つ上の段階に行けるはずです」
IoTで我が社のビッグデータを構築し、経営戦略に活かす
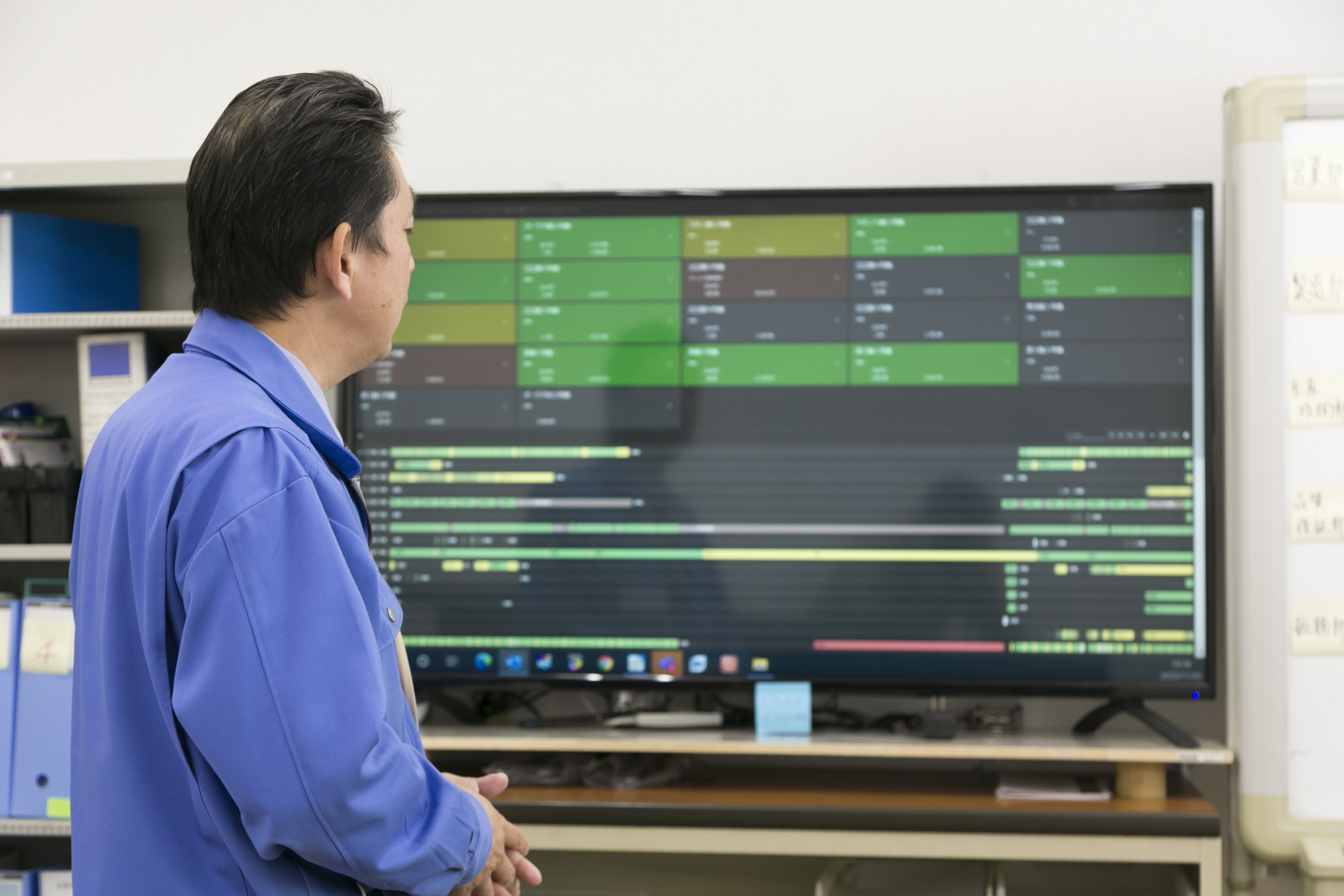
今後、IoTをどのように活用したいか、津田社長に聞いてみた。
「この2年間、デジタルソリューションさんに、『稼働率をグラフで見せてほしい』とか、『パーセンテージで見せて』とか、『8時から17時まで時間を区切って見せて』といった具合に、細かく要望してカスタマイズしました。そして、かなり現場の担当者が見やすく、使いやすいシステムに仕上がりました。日々積み重なっていくこれらのデータを“我が社のビッグデータ”として、活用できると考えています」
具体的には、どのような活用イメージなのだろうか。
「稼働率と売上データなどの経営情報と付き合わせて、次の経営戦略を立案するために役立てることができると思います。そして最終的には我が社のデジタルトランスフォーメーションにつなげていきたい。まだ具体的なイメージは浮かんできませんが、まずは生産効率を向上することに役立てていきたいですね」
今後、どのような『できない』を『できる』に変えていくのか。津田製作所のこれからの発展に期待したい。