4つの工場に分散する機械の稼働状況を“見える化”
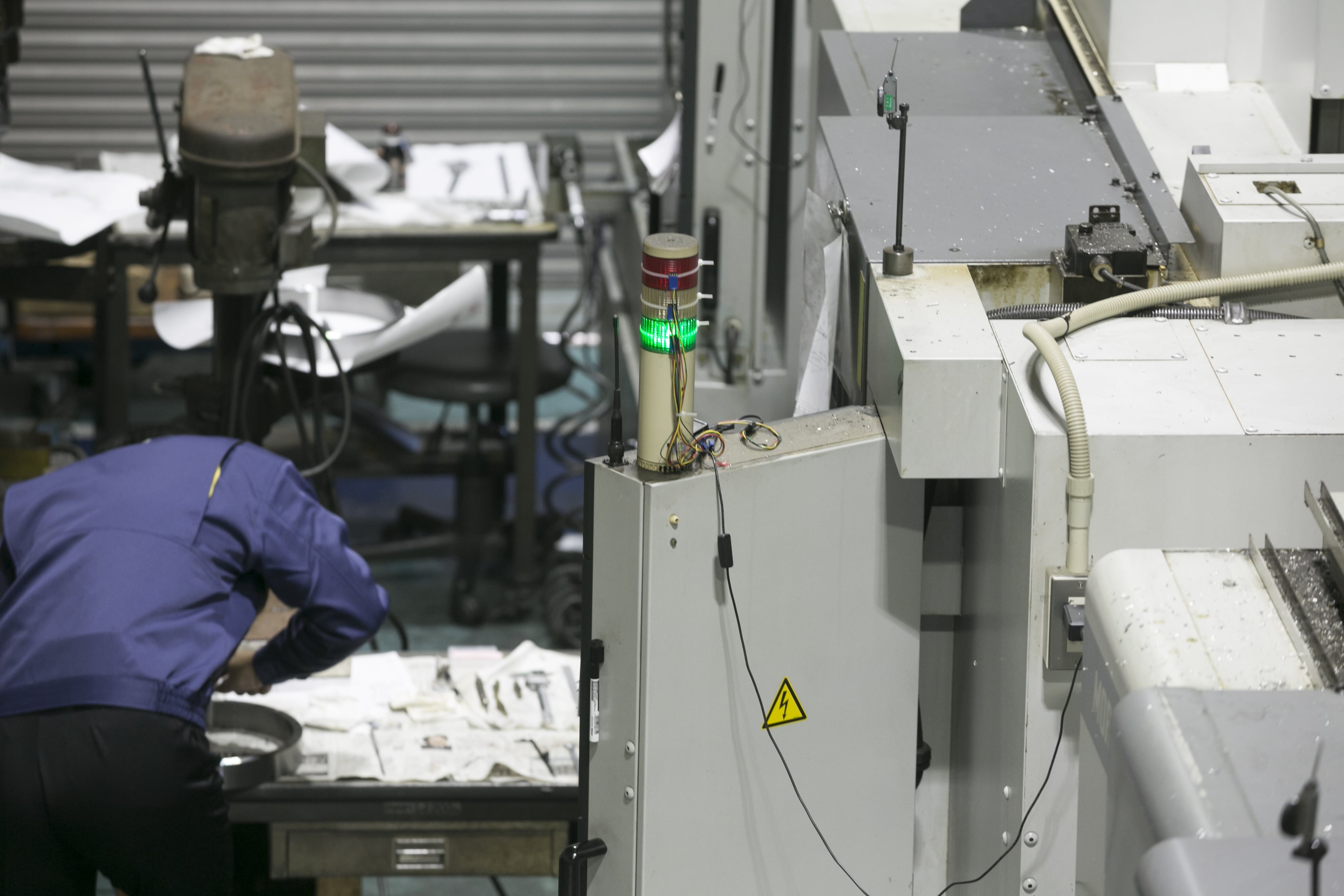
「よくクライアントから、『ここまで手間をかけなくても良かったのに』とか、『趣味で楽しみながら作り込んだような製品ですね』と言われます。渡された図面通りに作るだけなく、『手触りが優しいか』といった、細かいことにこだわって製品を作ってきました」
と語る松井社長。ものづくりに対するプライドと愛情が、現在の発展の礎となっている。
そんな広陵発條製作所がまず着手したIoTプロジェクトは、工場内の機械にパトライトと光センサーを取り付ける仕組み。これにより、各機械の稼働状況をモニターで一括表示することができるようになった。
「大手なら多額な初期投資をかけて、同一メーカーの機械のみで製造ラインを組み立てることができる。しかし、うちのような中小企業にはできません」
中小製造業は、工場内の機械のメーカーがバラバラであることが多い。創業時は少数の機械でスタートし、事業の発展に応じて必要な機械を買い足すケースが多いからだ。さらに、広陵発條製作所は工場を建て増しし、4ヵ所に離れている。これまでは全ての機械の稼働状況を、一度に把握するのは無理であった。 これを解決するために、デジタルソリューションが提案したのが、『機械の稼働状況の見える化』である。
知りたかったのは稼働率ではなく、トラブル発生状況
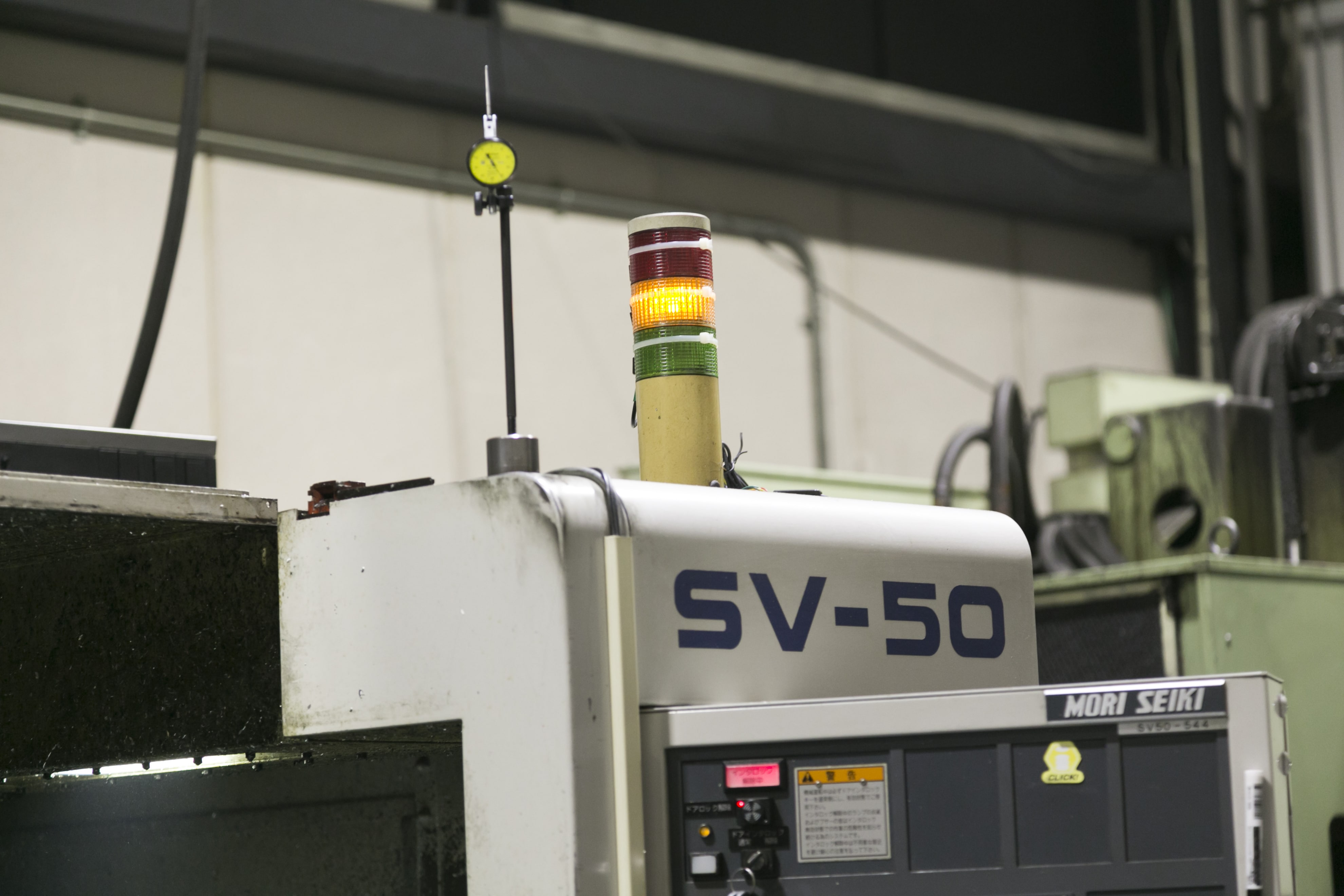
IoTで工作機械の稼働状況が把握できた時、大量生産を行なっている企業では「稼働中」の緑ランプの点灯状況が大きな関心事になる。しかし、広陵発條製作所の場合は事情が異なる。 「当社は単品モノの超小ロット生産ですから、稼働中の緑ランプよりも、『トラブル発生中』を示す『赤ランプ』の方が重要なんです」
その赤ランプがリアルタイムで把握できるようになり、何が変わったのか。 「今は赤ランプが着くと、すぐにベテラン社員が行って助けてやれるようになりました。IoT化する以前は、たまたまベテラン社員が赤ランプを見つけたら助けることができた。しかし、そうでない場合は、トラブルが発生した若い社員は焦ってパニック状態のまま、長時間一人で悪戦苦闘することが多かったんです」
このようにIoT化によりトラブルを復旧する時間が減り、社員のストレスも軽減した。さらに、 「過去のデータを振り返って、いつ、どんな頻度で赤ランプがついているのか、具体的な時間や数字で確認できるようになったのもありがたいですね。トラブルにつながる機械の不具合が見つかりやすく、対処しやすくなりました」
「測定具はどこに行った!?」
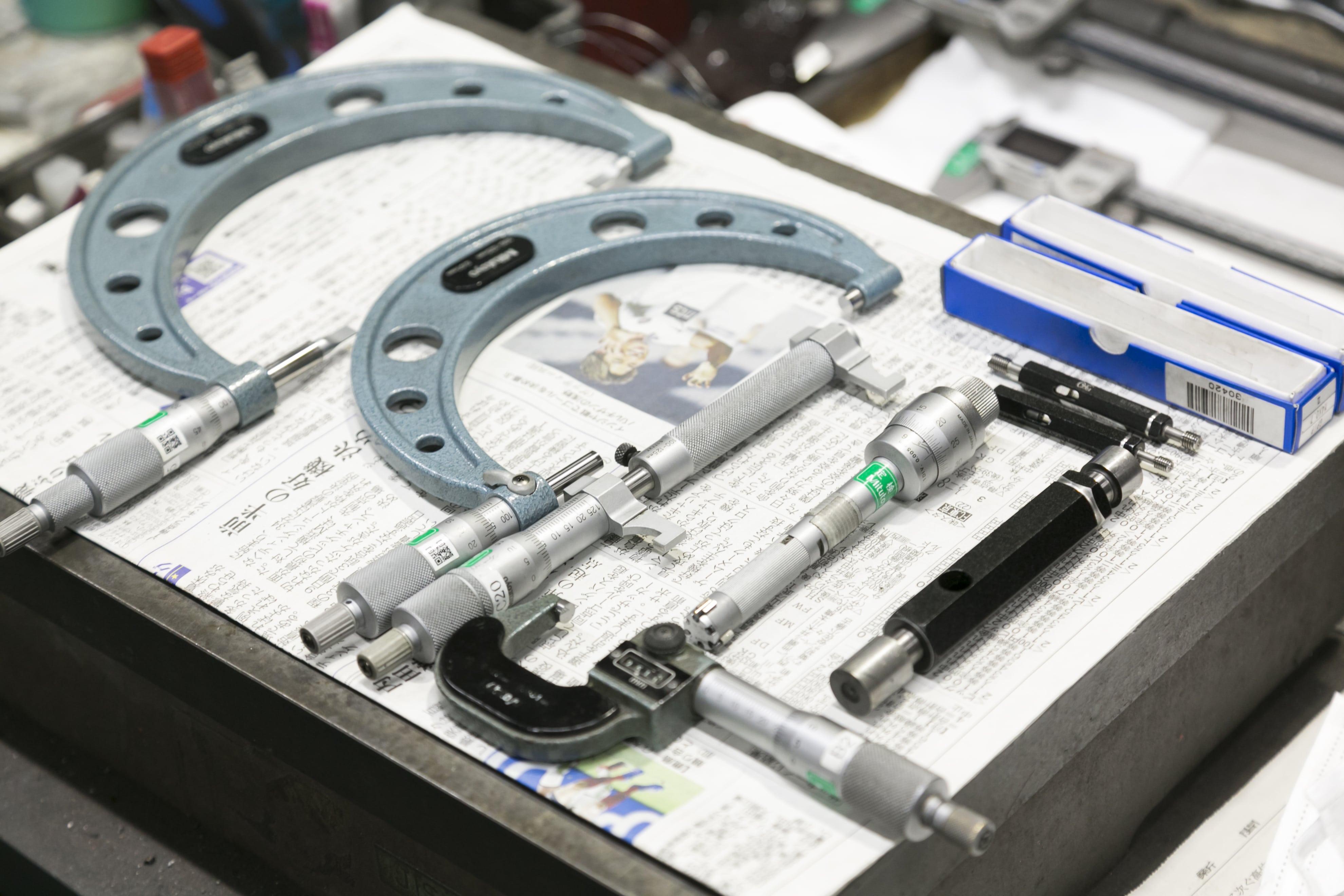
次に取り組んだのが、測定具のIoTによる管理である。
「当社の測定具は種類によっては1台しかありません。ある社員がそれを使いたくても所定の場所にない場合、他の社員たちに『使ってる?』と聞いて回っていました。そして使用している社員を見つけても、『ごめん、もう少し使うから待って』と、待たされて作業できない、なんていうことが起こっていました」
このようなロスをなくす改善は、IoT化以前も行なっていたが、
「人間の曖昧な感覚で、『あの測定具はよく使うので、もう1台購入しよう』という決断を行っていました。しかしIoTのお陰で、測定具の使用頻度が具体的な数値でわかり、無駄のない改善と投資が可能になりました」
IoTとAIがはじき出す『スプリングのレシピ』でオンリーワン企業に
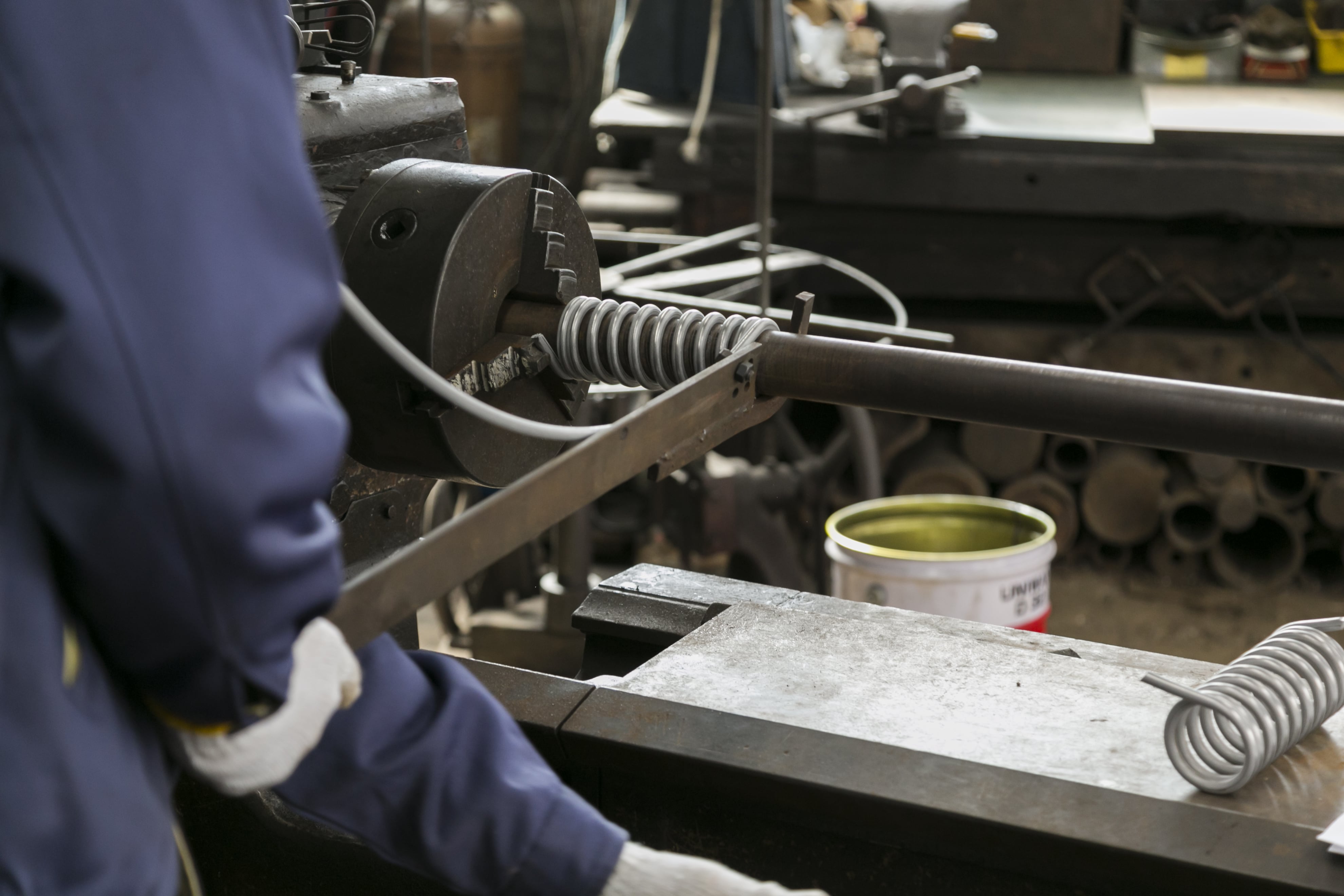
現在のスプリング製造は、担当者の藤岡さんが全て手作業で行なっている。
「スプリングは棒に金属製の線を巻きつけて作ります。初めての案件の場合、試し巻きをして、熱処理をして、試作品を作り、お客様の仕様に沿ったものができたか計測します。もし違っていたら、再び手の感覚で巻きの強さや、熱処理の温度と時間を変えて、また試作品を作ります。このようなことを繰り返して、仕様に近づけていきます」
これだけでもかなりの労力だが、まだ終わりではない。
「作り方が同じでも、同じメーカーの同じ材料を使っても出来上がりが異なることがあります。原因は、製造ロットナンバーによって硬さが違うからです」
現在は材料の性質が異なる毎に、藤岡さんが試行錯誤して巻き方を変えているそうだが、 「材料の傾向をIoTで計算し、『スプリングを作るためのレシピ』ができたらありがたいですね。IoTとAIを使って材料の性質を分析し、最短で巻き方がわかったら、他社が真似できないオンリーワンの技術になると思います」
IoTとAIで「多能工」を育てる
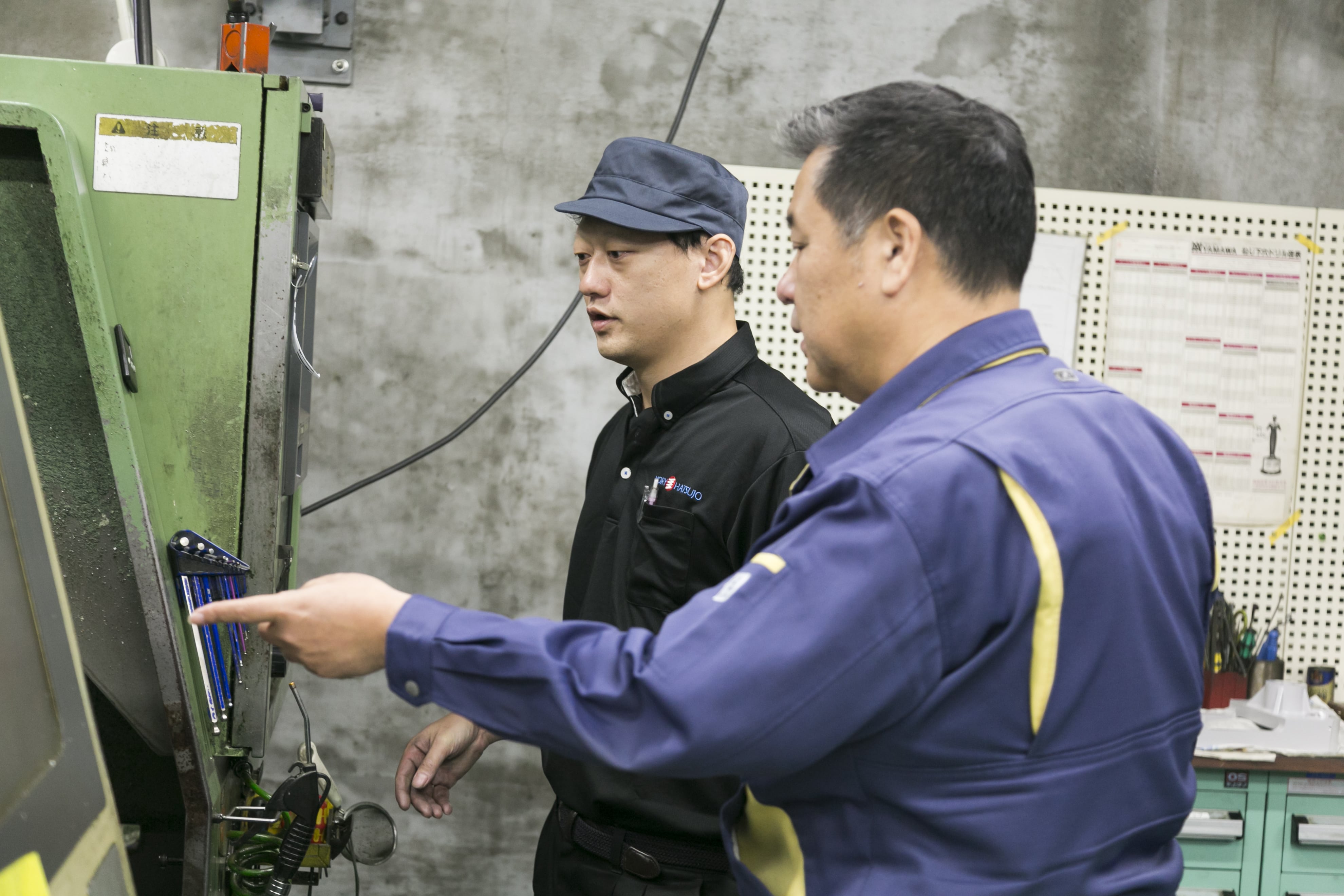
今後、IoTを使ってどんなことを挑戦したいか? 松井社長に問うてみた。
「組み立てや加工の順番を画像にとって、2回目以降はそれを見ながら組み立てができるようにしたい。最終的にはVRメガネを活用したいですね」
この願いの裏には、中小製造業ならではの悩みがある。
「中小企業はマンパワーが限られていますから、専任ができない。一人で何役もこなせる多能工が必要なんです。しかし、多能工になるには何年もかかります。早く多能工に成長してもらうために、若い社員にベテラン社員の作業を記録した動画を与えて同じ仕事ができるようにしたいんです。そして経験を積み、最終的に自分で動画や教材を作れる人になった時、その社員は多能工に成長していると思います」
IoTで、社員が友達に自慢したくなる会社に
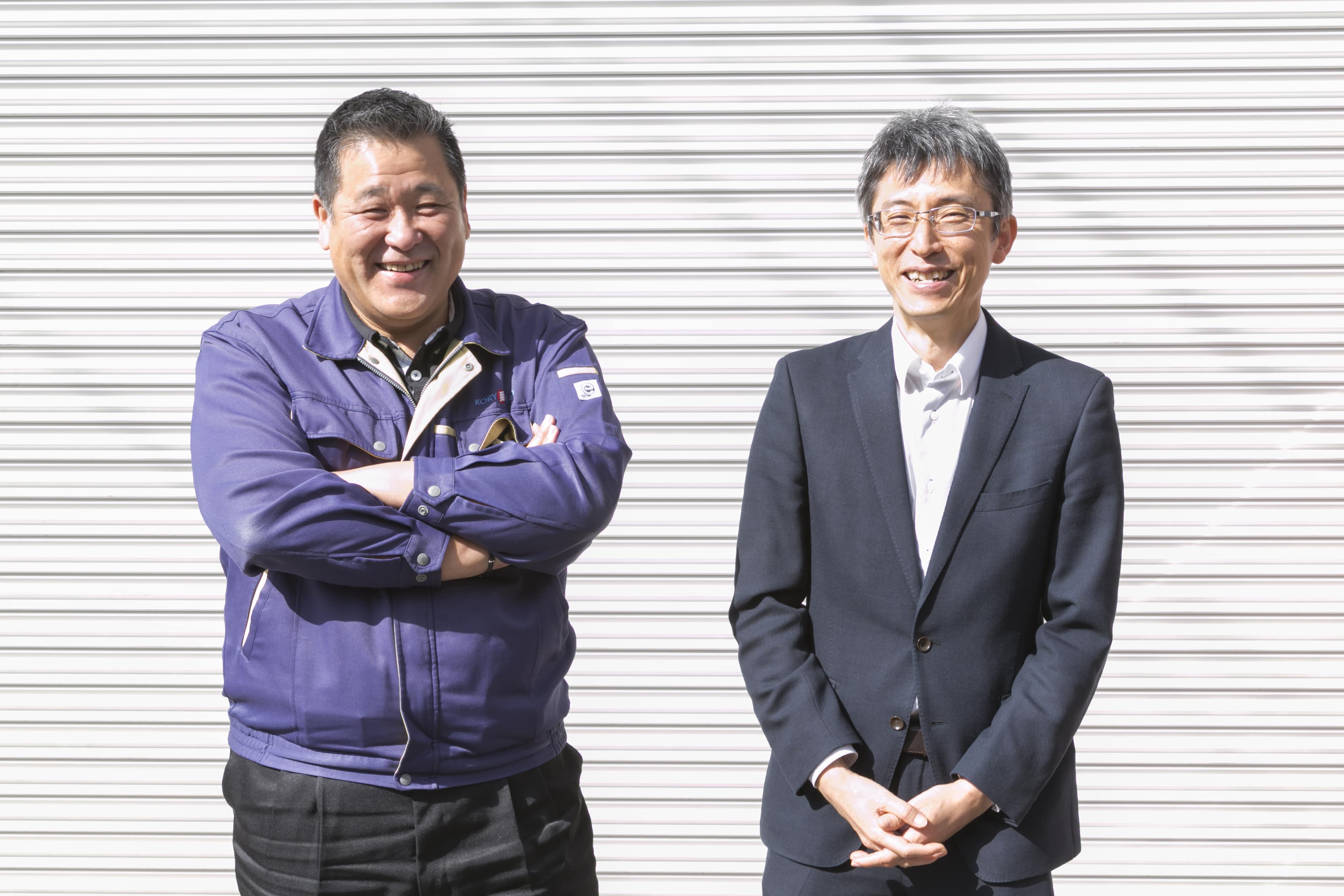
『この仕事が楽しくなるように』と語る松井社長には、社員と会社に対するこんな思いがある。
「社員が『勤めたい、残りたい、友達に自慢したい』と思えるような会社を作りたいんです」
それはどんな会社なのだろうか?
「社員が自分の存在感を感じられる会社ですね。『俺って、こんな難しい仕事もできるんだ!』といった達成感があると、仕事が面白くなり、技術力を高めながら勤めていけると思うんです。さらに給料も上がっていけば、社員は友達に自慢したくなると思うんですよ。そんな会社を作っていきたいんです。会社がより良く変化するために、IoTが役に立つのであれば、活用していきたいですね」